The Essential Guide to Plastic Molding in Metal Fabrication
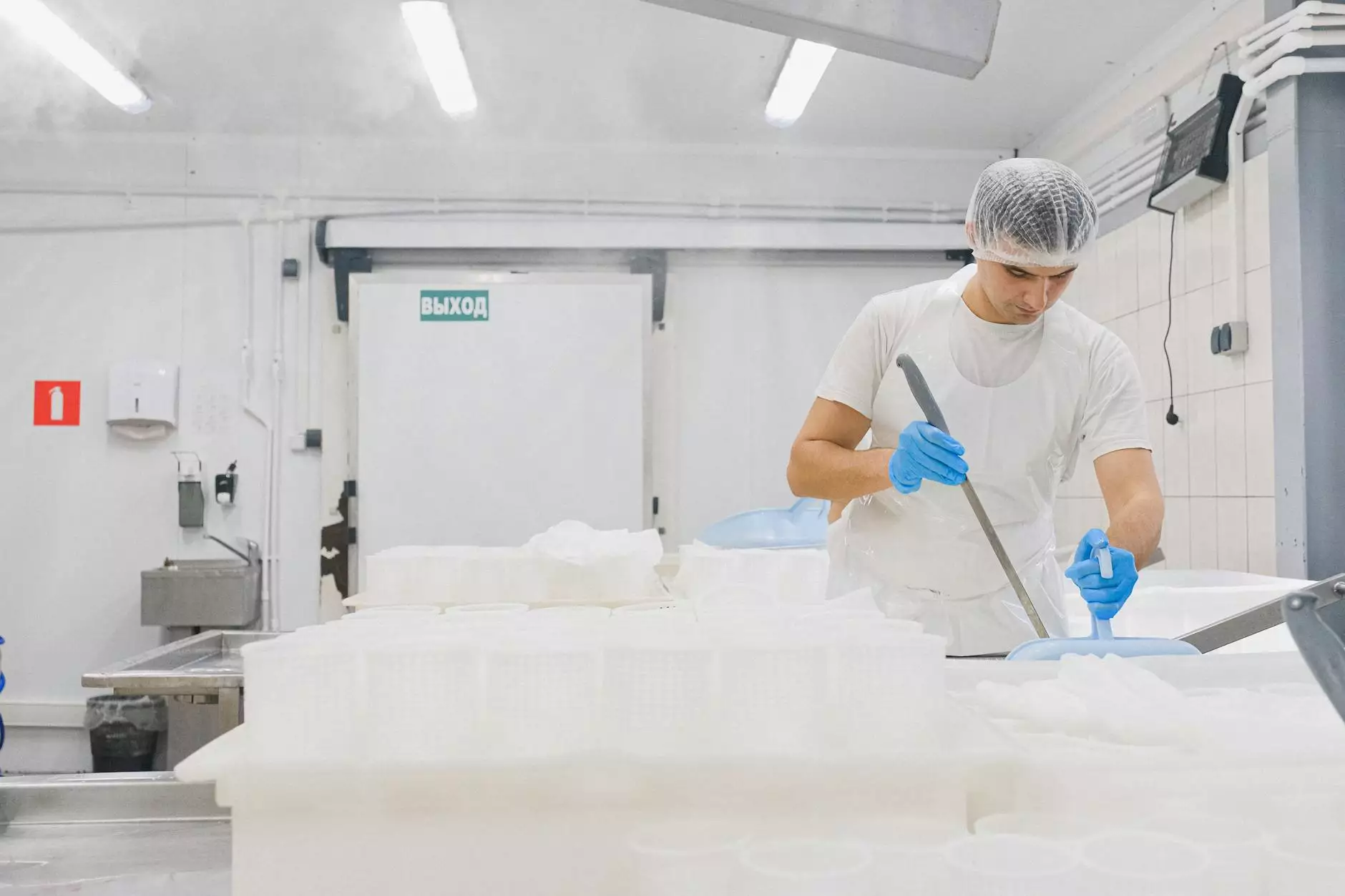
Plastic molding is a pivotal process in various manufacturing industries, particularly in the realm of metal fabrication. It allows for the creation of intricate designs and components that are both lightweight and durable, revolutionizing how we approach product design and production.
Understanding Plastic Molding
Plastic molding involves the process of shaping plastic materials into desired forms using a variety of techniques. It encompasses several methods, including injection molding, blow molding, and rotational molding. Each technique offers distinct advantages and is suited for different applications.
Types of Plastic Molding
- Injection Molding: This is the most widely used plastic molding process, where melted plastic is injected into a mold. It is highly efficient, allowing for the production of complex and detailed parts at scale.
- Blow Molding: This method is specifically used for hollow plastic parts. The process involves inflating hot plastic into a mold, resulting in lightweight products like bottles and containers.
- Rotational Molding: Ideal for producing large, hollow objects, this technique involves heating plastic in a mold that is rotated to evenly distribute the material.
The Role of Plastic Molding in Metal Fabrication
The integration of plastic molding in metal fabrication has transformed the industry. By combining metals and plastics, manufacturers can achieve new levels of innovation and functionality in their products.
Cost-Effectiveness
Utilizing plastic components within metal fabrications can significantly reduce production costs. The lighter weight of plastics compared to metals can lead to savings in shipping and handling, as well as lower material costs.
Enhanced Design Flexibility
With plastic molding, designers have greater freedom to create complex geometries that may be difficult or impossible to achieve with traditional metalworking techniques. This flexibility allows for a more creative approach to product design.
Improved Durability and Performance
Combining plastics with metals can enhance the overall durability of a product. Plastics can offer resistance to various environmental factors, such as moisture and corrosion, contributing to a longer lifespan for the metal parts they integrate with.
Key Applications of Plastic Molding in Metal Fabrication
From automotive to aerospace, the applications of plastic molding in metal fabrication are vast. Here, we explore some significant examples:
Automotive Industry
The automotive sector increasingly relies on plastic molding for components such as dashboards, bumpers, and lighting fixtures. Using molded plastics reduces vehicle weight, which in turn enhances fuel efficiency and lowers emissions.
Aerospace Applications
In aerospace, where weight reduction is critical, plastic molding is used for various interior components and some structural parts. The high strength-to-weight ratio of certain plastics makes them ideal for this demanding environment.
Consumer Electronics
Plastics play a vital role in the housing and components of consumer electronics. Plastic molding allows for intricate designs that not only meet aesthetic requirements but also protect sensitive electronic components.
Benefits of Plastic Molding in Metal Fabrication
The blend of plastic molding and metal fabrication presents a range of benefits that enhance production efficiency and product quality. Key benefits include:
1. Reduced Waste
Plastic molding techniques often result in less scrap material compared to traditional machining processes. This reduction in waste not only saves costs but also promotes environmental sustainability.
2. Fast Production Speed
Modern plastic molding techniques enable rapid production cycles, facilitating a faster time-to-market for new products. This speed is especially crucial in industries that must stay ahead of fast-changing consumer demands.
3. Easy Customization
Molded plastics can be easily customized in terms of color, texture, and even functionality, allowing for tailored products that meet specific customer needs.
Challenges in Plastic Molding for Metal Fabrication
While the benefits are substantial, there are also challenges associated with integrating plastic molding in metal fabrication processes.
1. Material Compatibility
Ensuring that the chosen plastics are compatible with the metals being used is crucial to the success of the final product. This compatibility affects adhesion, performance, and durability.
2. Design Constraints
Designers must account for the thermal expansion differences between metals and plastics. This requires careful planning to avoid warpage and other issues that can arise during production.
3. Manufacturing Complexity
Integrating plastic molding with metal fabrication can increase the complexity of the manufacturing process. Ensuring that all processes run smoothly requires a thorough understanding of both materials.
Future Trends in Plastic Molding
As technology advances, the future of plastic molding looks promising. Here are some trends that are shaping the industry:
1. Sustainable Practices
With a growing emphasis on sustainability, the industry is seeing an increase in the use of biodegradable and recycled plastics. This shift not only helps companies meet regulatory requirements but also appeals to environmentally conscious consumers.
2. Advanced Manufacturing Techniques
Emerging technologies such as 3D printing and additive manufacturing are being integrated with traditional plastic molding techniques, allowing for even more innovative designs and efficient production methods.
3. Automation and Robotics
Automation in plastic molding processes is on the rise, enhancing production speeds and consistency while minimizing human error. Robotics are playing an increasingly vital role in both the molding and assembly processes.
Conclusion
Overall, plastic molding is a transformative force in the field of metal fabrication. The combination of these two distinct materials not only provides manufacturers with endless possibilities but also meets the demands of modern consumers for lightweight, cost-effective, and durable products. As we look to the future, the integration of technology and sustainability will further enhance the capabilities of plastic molding in metal fabrication, ensuring its relevance for years to come.
For more information on how plastic molding can elevate your manufacturing process, visit us at deepmould.net.