CNC Precision Machining Factory: Leading the Future of Metal Fabrication
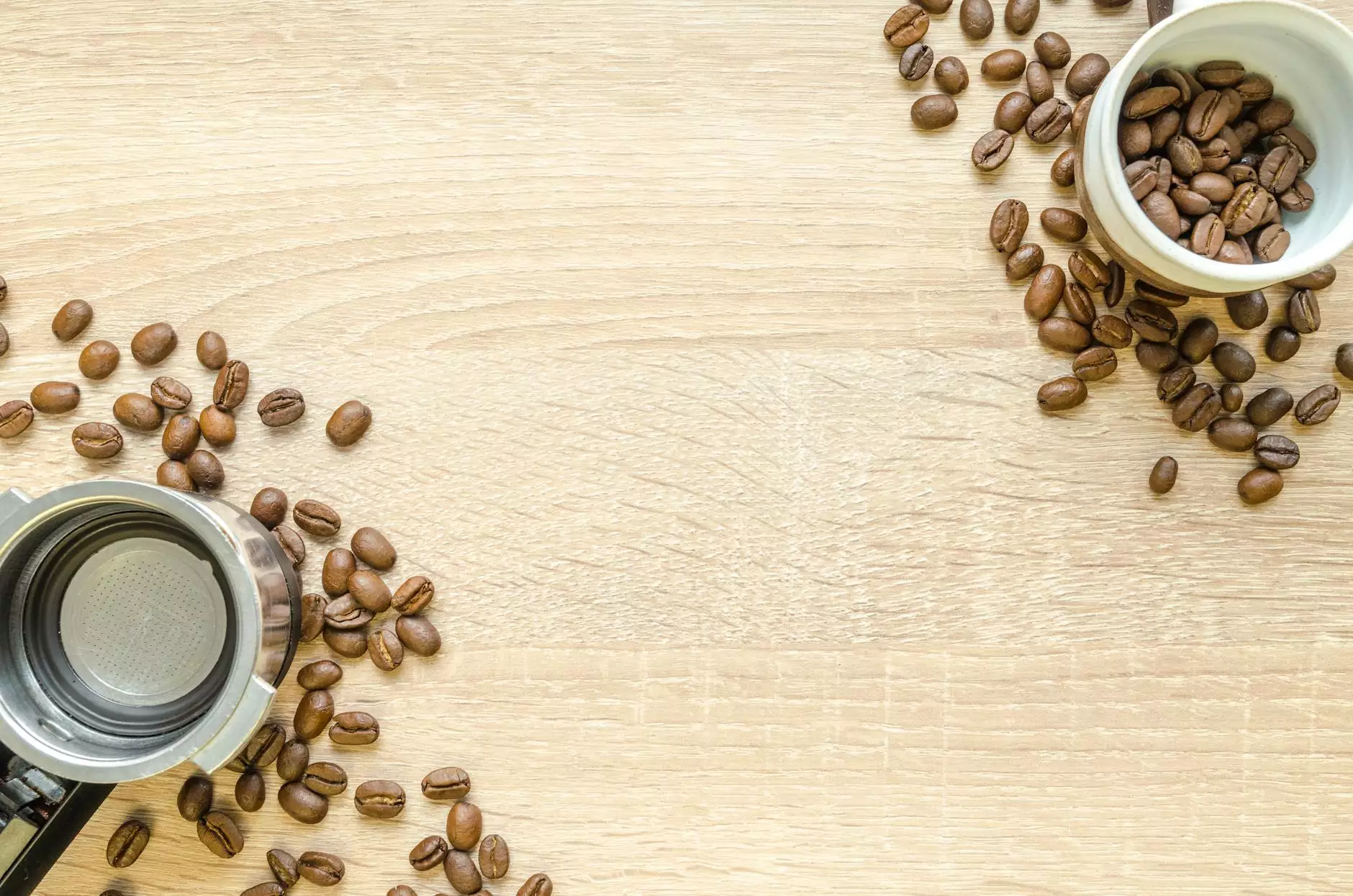
Understanding CNC Precision Machining
CNC (Computer Numerical Control) precision machining is a manufacturing process that involves the use of computers to control machine tools. This innovative technology allows factories to perform highly intricate and precise operations that are critical in the production of complex parts and components. A CNC precision machining factory specializes in this advanced manufacturing technique, delivering exceptional quality and accuracy.
Why Choose a CNC Precision Machining Factory?
There are numerous reasons why businesses opt for services provided by a CNC precision machining factory. Here are some of the most compelling benefits:
- High Precision and Accuracy: CNC machines can achieve tolerances as tight as one-thousandth of an inch, making them ideal for applications that require exact specifications.
- Efficiency: CNC machining enhances productivity by reducing the cycle time for production, thus allowing factories to produce more parts in less time.
- Consistency: Once a design is programmed, CNC machines can replicate the same product with uniform quality, minimizing the risk of human error.
- Material Versatility: CNC machining can work with a wide variety of materials including metals, plastics, and composites, making it suitable for different industries.
- Complex Geometries: The capabilities of CNC machines allow for the machining of complex shapes that would be difficult, if not impossible, to achieve using traditional machining techniques.
The CNC Machining Process
The process involved in a CNC precision machining factory is intricate and involves several well-defined stages. Here's a breakdown of the typical workflow:
- Design Phase: Engineers create detailed designs using Computer-Aided Design (CAD) software. This digital blueprint serves as the foundation for the machining process.
- Programming: The CAD designs are converted into a language that CNC machines understand, typically G-code. This code dictates how the machine operates.
- Setup: Prior to machining, the operator sets up the machine, installing the required tools and securing the material that will be machined.
- Machining: The CNC machine executes the program, cutting, drilling, or milling the material as defined in the design.
- Quality Control: After machining, parts are inspected for quality and adherence to specifications using precise measurement tools.
- Post-Processing: Additional processes such as finishing, coating, or assembly may be performed on the machined parts.
Applications of CNC Precision Machining
CNC precision machining plays a pivotal role across various industries. Here are some key sectors that benefit from this technology:
Aerospace Industry
In aerospace, components must meet stringent safety standards and precise specifications. CNC machining is used for producing parts such as turbine blades, brackets, and housings that require exact tolerances.
Automotive Industry
The automotive sector utilizes CNC precision machining for manufacturing critical components like engine blocks, transmission parts, and custom fittings. This technology not only enhances performance but also improves fuel efficiency through optimized designs.
Medical Devices
The production of medical devices demands high precision to ensure safety and reliability. CNC machining is employed to create surgical instruments, implants, and equipment that must comply with strict regulatory standards.
Electronics
The electronics industry relies on CNC machining to produce components such as housings, brackets, and circuit boards. The ability to work with small, intricate parts is crucial in this fast-paced sector.
Advantages of Partnering with a CNC Precision Machining Factory
Collaborating with a CNC precision machining factory provides businesses with several key advantages:
- Access to Expertise: These factories employ skilled machinists and engineers who understand the intricacies of CNC technology and can advise on design optimization.
- Scalability: CNC factories can easily scale production runs, allowing businesses to adapt to market demands without the need for significant investment in new equipment.
- Cost Efficiency: While initial setup and tooling may be expensive, CNC machining proves to be cost-effective in the long term due to reduced wastage and labor costs.
- Rapid Prototyping: CNC precision machining can be utilized to create prototypes quickly, allowing for faster product development and testing cycles.
- Supply Chain Optimization: A CNC factory can streamline the supply chain by providing faster turnaround times and improved quality assurance.
Choosing the Right CNC Precision Machining Factory
Selecting the right CNC precision machining factory is crucial for the success of your project. Here are essential factors to consider:
- Experience and Reputation: Research the factory's experience in your industry. Reviews and case studies can provide insights into their performance and reliability.
- Technological Capabilities: Assess the technology and machinery used in the factory. Advanced CNC machines offer better precision and productivity.
- Quality Control Measures: Inquire about the factory's quality assurance processes and certifications. ISO certification is a positive indicator of quality standards.
- Communication: Establishing a clear line of communication is vital. The factory should be responsive and open to discussions regarding designs and specifications.
- Cost Transparency: Ensure that the factory provides transparent pricing and detailed quotes to avoid any unexpected expenses.
The Future of CNC Precision Machining
As technology continues to advance, the CNC precision machining factory landscape is evolving rapidly. Innovations such as Artificial Intelligence (AI), Internet of Things (IoT), and Industry 4.0 are shaping the future of manufacturing. Here are some trends to watch:
- Smart Manufacturing: Automation and real-time monitoring will enable factories to optimize processes and reduce downtime significantly.
- Advanced Materials: The introduction of new, lightweight, yet durable materials is expanding the horizons for CNC precision machining.
- Sustainability: Factories are increasingly focusing on environmentally friendly practices, including waste reduction and energy-efficient machining operations.
- Customization: The demand for personalized products will lead to more agile and responsive manufacturing processes.
- Integration of AI and Machine Learning: These technologies will enhance predictive maintenance, improving machine longevity and performance.
Conclusion
In conclusion, a CNC precision machining factory is an indispensable partner for businesses aiming to produce high-quality parts with unmatched precision. By understanding the processes, advantages, and applications of CNC machining, companies can make informed decisions that drive their success in today’s competitive landscape. As technology advances, these factories will continue to play a critical role in the future of manufacturing, leading the way towards innovation and efficiency in industry practices.
For businesses seeking exceptional CNC precision machining solutions, look no further than DeepMould.net. With a commitment to quality and excellence, we are here to cater to all your metal fabrication needs.