Comprehensive Insight into Injection Plastic Molding
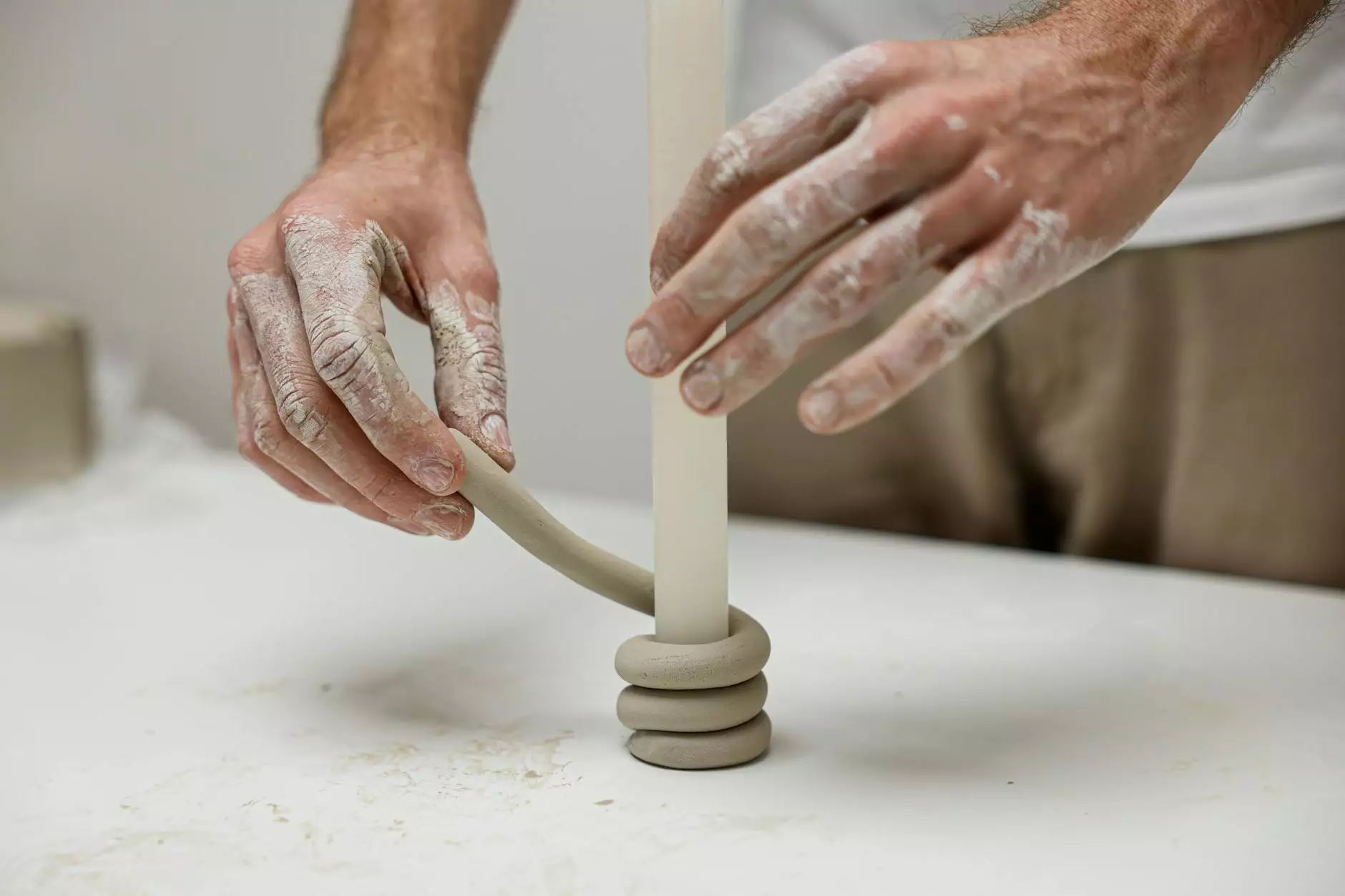
Injection plastic molding is a revolutionary manufacturing technique that has reshaped various industries by enabling precise, high-volume production of plastic parts. As we delve into this sophisticated process, we will uncover its mechanisms, benefits, applications, and how it stands as a cornerstone for companies involved in manufacturing.
Understanding Injection Plastic Molding
At the core of injection plastic molding lies a simple yet effective process. It involves injecting molten plastic into a mold to create a desired shape. The process boasts numerous advantages, making it a popular choice among manufacturers worldwide. Below, we'll break down this method to better understand its workings:
The Injection Molding Process
- Material Preparation: The process begins with the selection of plastic material, which is then fed into a hopper.
- Melting: The plastic granules are heated until they reach a molten state.
- Injection: The molten plastic is injected into a precision-engineered mold under high pressure.
- Cooling: The plastic is allowed to cool, solidifying into the desired shape.
- Mold Opening: Once cooled, the mold opens, and the finished part is ejected.
- Finishing: Additional finishing processes, such as trimming and surface treatment, may follow.
The Key Elements of Injection Plastic Molding
Several factors contribute to the efficiency and effectiveness of injection plastic molding:
- Materials: A variety of thermoplastics can be utilized, including polypropylene, polyethylene, and polyvinyl chloride (PVC).
- Mold Design: The mold's design is crucial, as it dictates the detail and intricacy of the final product.
- Temperature Control: Maintaining the right temperature is essential for consistent material flow and part quality.
- Cycle Time: The speed at which the entire process is carried out affects productivity.
The Benefits of Injection Plastic Molding for Businesses
Understanding the benefits of injection plastic molding is crucial for businesses looking to innovate their manufacturing processes. Here are several advantages this technique offers:
1. High Efficiency and Speed
One of the standout features of injection plastic molding is its ability to produce large quantities of parts in a short time. The machine can operate continuously, making it ideal for mass production. This high-speed operation translates into lower production costs and increased profitability.
2. Precision and Reproducibility
The use of sophisticated molds allows for high precision in manufacturing. Each molded part adheres closely to the specified dimensions, ensuring consistency across batches. This level of reproducibility minimizes waste and enhances product quality.
3. Versatility of Materials
Injection molding isn’t limited to a singular type of material. Manufacturers can choose from a wide array of plastics, giving them the flexibility to develop a variety of products, from sturdy, impact-resistant casings to lightweight components.
4. Reducing Waste and Cost
By optimizing the injection molding process, businesses can reduce material waste. Excess plastic can often be recycled and reused in subsequent production runs, further driving down costs and contributing to sustainability efforts.
5. Complex Designs Made Easy
Injection molding allows for the creation of complex shapes and designs that would be difficult or impossible to achieve with other manufacturing techniques. The detailed molds can incorporate features such as texturing, logos, and even intricate internal geometries.
Applications of Injection Plastic Molding
The versatility of injection plastic molding means that it finds applications across numerous industries. Here’s a closer look at where this technique is utilized:
1. Consumer Products
The consumer goods industry heavily relies on injection molding for producing everyday items such as containers, toys, and household goods. The ability to produce colorful, durable plastic products allows companies to cater to diverse consumer needs.
2. Automotive Industry
The automotive sector benefits from injection molding for creating lightweight, durable parts that contribute to vehicle performance and aesthetics. Components such as dashboards, panels, and gearing systems are often manufactured using this process.
3. Medical Devices
In the medical field, precision is paramount. Injection molded parts provide the necessary reliability and cleanliness needed for devices like syringes, inhalers, and surgical instruments, ensuring that patient safety is never compromised.
4. Electronics
From casings for smartphones to intricate components within computers, the electronics industry sees significant benefits from injection molding. The ability to mold high-temperature resistant parts further solidifies its role in tech manufacturing.
Challenges in Injection Plastic Molding
While there are many advantages to injection plastic molding, the process is not without its challenges. Understanding these hurdles can help businesses navigate the waters more successfully:
1. High Initial Costs
The upfront investment for molds and machinery can be quite significant. For new businesses, this can pose a financial barrier to entry and necessitate a well-thought-out financial strategy.
2. Mold Maintenance
Maintaining molds to ensure quality production can require additional resources and expertise. Neglecting mold upkeep can result in defects in the produced parts, leading to increased waste and costs.
3. Complexity of the Setup
Setting up the machinery and aligning processes for optimal output requires skilled labor and technical know-how. Training personnel is essential to minimize human error during production.
Future of Injection Plastic Molding
As technology continues to advance, the future of injection plastic molding looks promising. Here are some trends shaping the industry:
1. Sustainable Practices
As more businesses become aware of their environmental impact, there's a push towards using recycled plastics and eco-friendlier materials. Innovations in biodegradable plastics are also gaining traction, allowing injection molding to remain relevant while promoting sustainability.
2. Automation and Technology Integration
The integration of automation and IoT technologies will further improve production efficiency. Smart factories, equipped with advanced robotics and data analytics, allow for real-time monitoring and enhancement of the molding process.
3. Customization and 3D Printing
The rise of 3D printing technology presents a unique opportunity for injection molding to evolve. Manufacturers can utilize 3D printed models to test molds quickly and efficiently, ensuring better fit and function before large-scale production begins.
Conclusion
Injection plastic molding stands as a pivotal manufacturing process that enables businesses to create high-quality, precise plastic parts with efficiency and speed. From its myriad advantages to its diverse applications, this process is essential in modern manufacturing. By understanding the intricacies of injection molding, businesses can leverage this technology to enhance their product offerings and position themselves ahead of the competition in today's dynamic market.
For more information on injection plastic molding and how it can transform your manufacturing capabilities, visit deepmould.net.